A major car manufacturer in South America needed a new solution to improve their engine dress up assembly. A solution that would address expansion and operator guidance limitations in their current Programmable Logic Controller, PLC, system. The solution provided by Atlas Copco not only solved these issues, it enabled annual savings of over €1,000,000.
Engine dress up is the manufacturing process where previously assembled motor modules and components are further assembled to create a finished drive unit. In this process, an automotive manufacturer was facing challenges related to their PLC solution. A PLC is a programmable computing device used to manage electromechanical processes and is sometimes referred to as an industrial PC.
In this specific case, the car manufacturers’ existing PLC solution put constraints on the operations flexibility and operator efficiency. In order to expand the PLC error-proofing solution to other assembly lines, large investments were required. The PLC also lacked sequence and part control as well as part verification subject to product variants further inhibiting production flexibility. Finally, it was not able to effectively guide station operators in rework. The conclusion was therefore that the existing PLC solution was inflexible, inefficient and caused high rework and operator training costs.
An onsite-team from Atlas Copco was engaged to evaluate the existing production process and renewal needs. The solution suggested was to take control of the operator station and implement a smart and fully integrated software platform. A platform offering the following advantages:
- Integration with existing MES, PLCs and measurement devices
- Advanced assembly reporting
- Centralized configuration of all assembly stations
- Full error-proofing process
- Product identification and tracking of all relevant results
The outcomes
The bottom-line operational benefits of the implemented solution speak for themselves:
€471,000
Annual rework cost savings
€65,000
Annual reduction of training costs for operators thanks to 90% reduced training time
€619,000
Annual cost savings due to reduced inefficiency measured as time loss for cycle time, problem identification and introduction of new products or variants, time loss due to for instance reading printed instructions, failure in part selection et cetera, waste of energy, tools and tightening components such as nuts and bolts
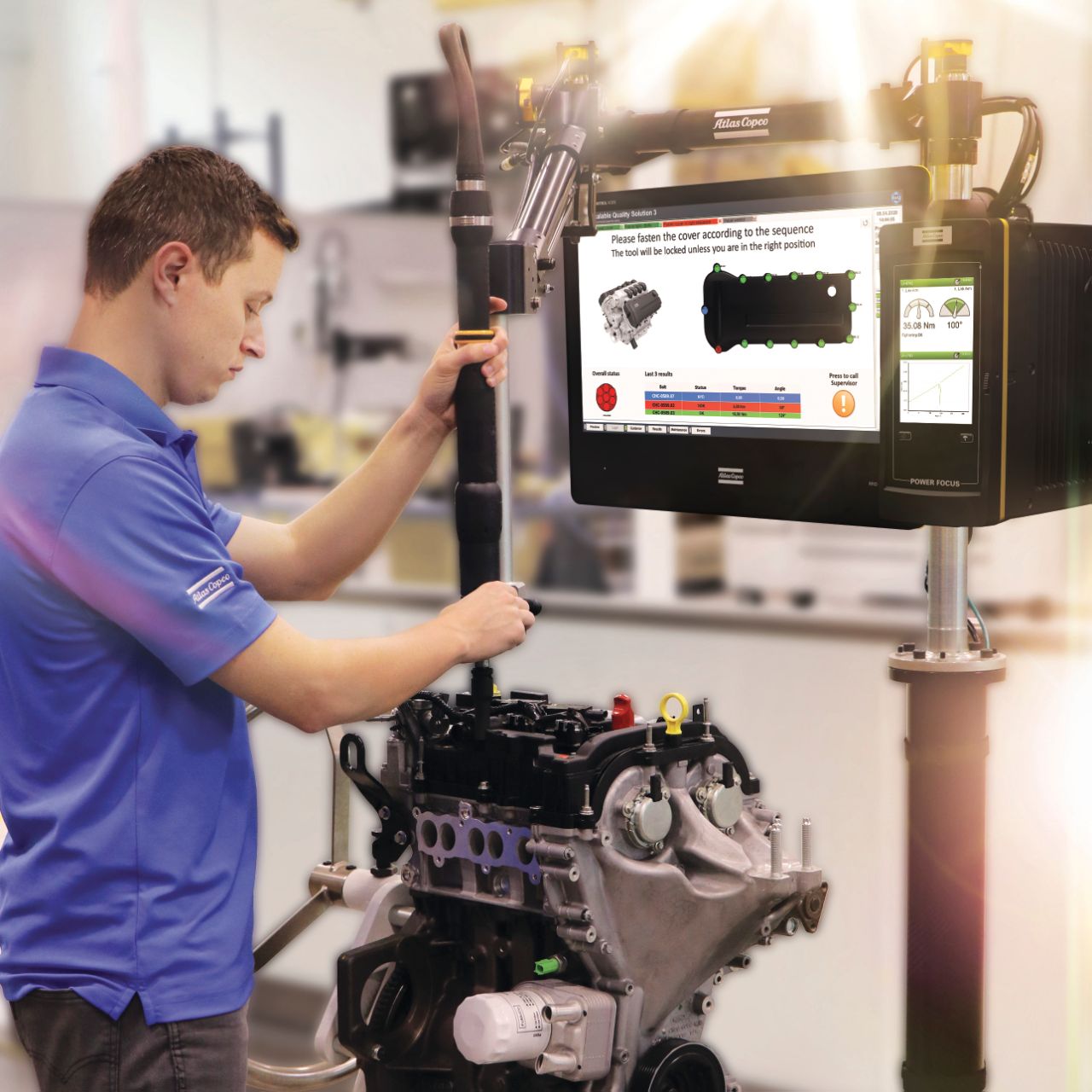
“Station Controlled” is the second of five steps in the Atlas Copco Smart Integrated Assembly concept. A comprehensive Industry 4.0 offering for industrial manufacturers looking to transform and implement smarter and more efficient production in Smart Factories. It includes smart connected assembly tools for factories and field operations, fully integrated assembly line solutions from design to production, as well as a unique set of data driven services.
To learn more about how Atlas Copco can help through the road to the Smart Factory, visit our page Station Controlled – Empower your operators to do a better job. Or get in touch with us today!